Facilitating a Culture of Continuous Improvement
Overview
- Provided skills to enable teams to quickly implement process improvements.
- Embedded a workplace culture and shared language of Lean Process improvement.
- Improved communication and teamworking between departments.
- Promoted innovation and idea generation using data driven decision making.
Background
PPS Returnable Equipment Solutions supply returnable transit packing to the Food and Drink Sector. They wash and sterilise packaging to the highest of standards and return to the customer, offering a sustainable minimal waste solution, reducing single-use packaging and promoting a circular economy.
Established in 2001 the business has grown rapidly, and they are now looking to cement their position by developing world class operations. Fundamental to this vision is to establish a culture of process improvement with a shared language and vision of operational excellence.
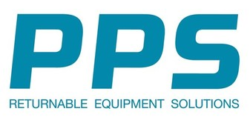
Production Support 56 delivered an engaging Lean Six Sigma training program for our staff at PPS Midlands across various teams in sales, production and finance. All the team members thoroughly enjoyed the course which gave each department a clear understanding of Lean concepts and a host of ready to use tools.
The course was delivered very precisely with great enthusiasm and fun team working exercises which helped to demonstrate some of the trickier concepts of variation and inconsistency and how these can be improved using Lean and Six Sigma tools
Objectives
- Lean Six Sigma training: Delivery of process improvement training across the company. Providing the staff with the main concepts and techniques of Lean Six Sigma.
- Common language: Provide staff with a common language so they can understand and engage with the current process improvement activities.
- Process improvement skills: Help staff identify opportunities for improvement and to make a business case using data
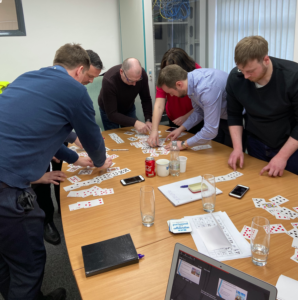
The Solution
- PS56 worked with the Operations Director to identify the key skills and tools relevant to the business.
- Delivered Lean Six Sigma White belt program to multi-levelled teams with an initial focus on workplace organisation, structured problem solving and process improvement, compliant with the IASSC standard for Lean Six Sigma training.
- A training evaluation exercise was carried out in alignment with the current business objectives to identify suitable candidates for progression to advanced Lean Six Sigma training.
The Benefits
Up Skilled Staff
Newly learned skills enabled teams to immediately implement workplace organisation improvements.
Lean Culture
Trained members shared the common language of Lean Six Sigma and have a collective understanding of the concepts and methods used for improving processes.
Improved Team Working
Team based exercises have enhanced employee inclusion, improved communication and team co-working between departments.
Practical Training
Training has enabled team members to identify opportunities for improvement and collect relevant data to make a business case.