Increasing Laboratory Capacity and Compressing Lead Times
Overview
- Decreased Laboratory testing lead time by 86%.
- Reduced operational costs by 20% year on year, 3 years consecutively.
- Improved test accuracy and repeatability, reducing variation by 90%.
- Levelled experimental process flow eliminating major bottlenecks.
Background
Metalysis was developing a novel and disruptive process for the production of speciality metal powders. The Research & Development arm of the business played a vital role in supporting both process development and testing the feasibility of new products. Each R&D test was conducted by a small team of highly skilled technicians, carrying out around 300 tests each year.
The problem was that each test took three weeks to complete, which was too long a feedback loop for the business.
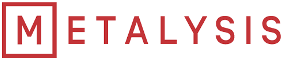
Mike was instrumental in producitonising the Metalysis R&D facility. He was able to identify weakness in the system and successfully put practices in place to solve them.
Objectives
- Improve consistency: Experiments carried out within a sequence of trials produced highly variable results. This meant that it was almost impossible to make reasonable comparisons or draw meaningful conclusions.
- Standardisation: There was no standardised system for requesting experiments, reporting of process data and analytical results. This led to frequent experimental errors, lost or missing data and loss of important learning.
- Compress lead times: Each test took at least three weeks to complete, from design to delivery of results. It was often the case that by the time the results were made available, the purpose for the tests had been forgotten or was no longer relevant to the project.
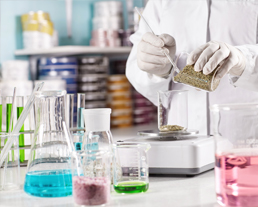
The Solution
The best laboratory practices were identified through consultation with stakeholders, scientists, analysts and technicians. All processes and systems were standardised in terms of the equipment, tools, methods and materials used. Using a blended learning approach, a culture of continuous improvement was embedded in the team which resulted in an excess of four hundred improvement events occurring over a three year period.
The Benefits
Compress Lead Times
The time it took to prepare, perform and analyse the experiments was reduced from a staggering 3 weeks to 3 days.
Reduced Costs
Operational costs were reduced by more than 20% for three consecutive years.
Smoothed Process Flow
Reduced overburdening both equipment and staff by levelling the daily workload facilitating smoother laboratory process flow.
Improved Quality
Standardisation of work practices increased both the accuracy and repeatability of the test results, reducing the statistical variability from 30% to 3%.
Increased Capacity
Increased the capacity of the laboratory to complete 80% more experiments, without requiring any additional resources.
Increased Confidence
Increased the capacity of the laboratory to complete 80% more experiments, without requiring any additional resources.