Supporting Investment Decisions with Simulation for Improvement
Overview
- Identified critical process bottlenecks and solutions to resolve them.
- Demonstrated an increased line output by 55%.
- Verified that alternative working patterns increase output by 35%.
- Identified process equipment to add product line capability.
Background
Norvik Ltd are an established food producer specialising in the manufacture of speciality fish cakes with an extensive portfolio of both breaded and bespoke contract processed products. The business had come under new ownership and had plans to modernise production with new process equipment in order to diversify their product range and increase process throughput.
Norvik were evaluating the benefit of investing in new equipment such as fryers, freezers, and storage), optimising current processes and changing shift patterns to increase daily capacity.
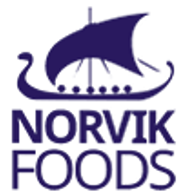
Objectives
- New equipment: A lot of the equipment was old and obsolete, other equipment had insufficient capacity and limited capability. Norvik had identified several items of new equipment to upgrade their line.
- New shift patterns: The staff were underutilised for parts of the day, the new owners wanted to identify more efficient shift patterns to increase throughput without over burdening the staff’s workload.
- Evaluate line performance: The new owner wanted to assess the performance of the production line and identify bottlenecks and areas for improvement.
The Solution
PS56 constructed a dynamic computer model of the Norvik fishcake production process to assess current line performance and identify process bottlenecks and uneven flow. The model was also utilised to similate the addition of new equipment and measure performance.
The model was used to evaluate multiple scenarios:
- New equipment (fryer, freezer, storage).
- Optimised processes (mixing).
- Alternative shift systems.
- Staggered breaks.
The Benefits
Process Insight
The model offered detailed insight into current production line performance and identified and quantified where improvement can be made.
Return on Investments
The cost-benefit and payback period of new equipment was calculated allowing the new owners to make informed decision about where and when to invest in the production line.
Increased throughput
Simulation for Improvment provided a detailed plan to balance the production line with the potential to increase throughput by 55%.
Increased Capacity
The model demonstrated that proposed changes to working patterns could increase daily production by 35%.
Planned Growth
The simulation provided a detailed growth plan to increase production by 25%.
Clear Solutions
Technical challenges associated with the growth plan were identified and practical solutions given prior to any implementation.