Using Manufacturing Simulation to Test and Validate New Plant Design
Overview
- Confirmed plant design meets client’s specifications.
- Identified ~£1million of capital savings.
- Communicated new plant design to all stakeholders.
- Allowed clients to test the new design.
- Removed operational bottlenecks at design stage
Background
Allied Protek are an Engineering company that provide project management, and Engineering & Design services. They work in numerous sectors including, Food & Drink, Chemical and Defence.
They were commissioned to conduct a front-end engineering design study for a fertiliser manufacturer, the aim was to automate the manufacturing process and reduce raw material inventories. To support their design, they needed dynamic calculations of inventory levels and vehicle movements.
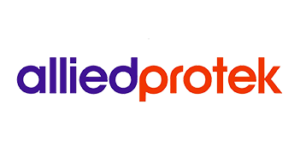
Production Support 56 were brought in late to the project and quickly produced an accurate simulation of our design which was run with the client historic production data. They proved the design met all our clients’ requirements and helped us optimise and removed significant costs. The client loved the model demonstration and subsequent what-if games.
Objectives
- Raw material storage- The client wanted sufficient storage of raw materials to maintain production and keep a reserve of a days’ worth of stock. This required a dynamic calculation that accounted for the variation in consumption and delivery of materials throughout a normal working day.
- Vehicle movement and queuing- The flow of traffic in and around the plant needed improving and the queuing of tanker vehicles on public roads minimised. This was evaluated by creating a model that triggered vehicle and material movements.
- Maintain current production capacity- The client’s brief was to maintain the current plant’s capacity. This was difficult to calculate as there were shared resources, varying cycle times, many moving parts and each product was bespoke.
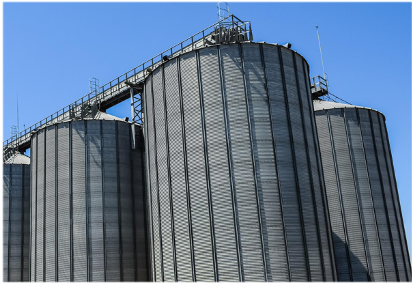
The Solution
Production Support 56 created a dynamic computer model of Allied Protek’s design and ran it using the client’s historic production data. The model simulated four major operations.
- Administration- Setting production schedule and managing raw material inventories.
- Raw materials delivery- Delivery schedule, arrival, unloading and storage of raw materials.
- Product manufacturing- Withdrawal and transfer of raw materials, manufacture of product, and loading of distribution tankers.
- Product distribution- Clean down, loading, distribution and return of product tankers.
The model could test numerous scenarios by configuring it through an excel spreadsheet, and selecting the required production season (spring, summer, or autumn). The data from interesting scenarios could be exported to an excel spreadsheet for further analysis
The Benefits
Validated Growth Plan
The simulation confirmed that the new design capacity met the client’s expectations. It was also used to develop a growth plan to increase capacity by 25%.
Design Optimisation
The model provided operational insight into new plant design. Identified bottlenecks and helped optimise the engineering design.
Slashed Capital Costs
Identified underutilised equipment providing ~£1 million of savings from the capital project costs.
Share Design
Communicated new design to clients and all stakeholders.
Operational Insight
Provided operational insight into new plant design.
Scenario Testing
Provided an environment to test different scenarios, build confidence and provide useful feedback for the design team.