Process Improvement
Successful delivery of your process improvement project
We provide the extra expertise and resources to get your improvement projects successfully completed quicker and effectively without impacting on your day-to-day operations
Start Your Improvement
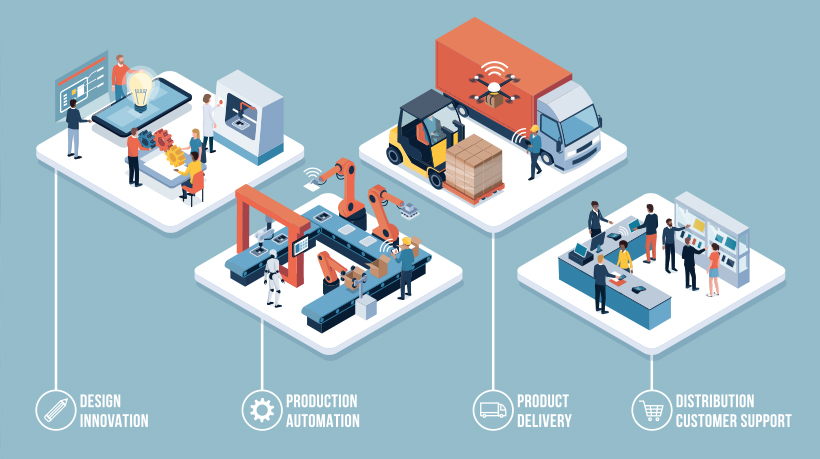
Improving Manufacturing Processes
Process improvement is a crucial step for any organization looking to increase efficiency, reduce costs, and improve product quality. It’s a continuous effort that requires an ongoing commitment and attention towards a shared vision of operational excellence and best manufacturing practice. By focusing on key areas for improvement, collecting data, and implementing a plan, organizations can achieve their goals and deliver sustainable business growth.
Spotting Waste and Identifying Value
When starting out on any improvement project its crucial to understand how the current system is performing. Once this is understood you can then compare the current performance against a target or goal and identify solutions to bridge the gap.
We provide a technical gap analysis of your current production capabilities against where you need to be. We do this by constructing a detailed process map of your current and future operations. This provides you with a rich and detailed insight into your production and highlights activities which add value and those that are a waste.
Process Improvement Tools
The world is awash with process improvement tools from the realms of lean manufacturing, six-sigma, quality, and industrial engineering. It’s easy to get bogged down with the vast choices available and all the jargon which goes along with it, our team of experienced professionals will help you cut through the nonsense and help deliver the improvements you need, in the most effective way.
Our team appreciates that each business is unique, and there is no one-size fits all solution when it comes to lean manufacturing. That’s why we work with you to identify your specific needs and goals and help you choose the right tools to achieve them. We can provide a variety of tools that can help you achieve your goals, from value stream mapping and Kaizen events to 5S and SMED analysis. Each tool has its own benefits and can be used to address specific issues or opportunities within your organisation.
Continuous Improvement Culture
Continuous improvement is a vital component of any successful organization, and creating a culture that fosters it can lead to increased productivity, quality, and employee engagement. At the core of a culture of continuous improvement is the belief that there is always room for improvement, no matter how well things are going. It requires a mindset shift from focusing solely on achieving goals to identifying and addressing opportunities for improvement.
To develop a workplace culture of continuous improvement, it is essential to involve employees at all levels of the organization. Employees are the ones who are on the front lines, and they often have valuable insights into how to improve processes and procedures. Encourage them to share their ideas and suggestions and empower them to take ownership of their work.
We offer a variety of tailored learning and development programs to help you develop a culture of continuous improvement, including training programs, practical workshops and leadership coaching. We work with you to identify your organization’s specific needs and goals and provide customized solutions that fit your unique situation.
The guys at PS56 made some cracking procedures which we use all the time especially with the new staff. It means I’m not on the shop floor every 10 minutes and I’ve got more time to deal with my big clients. They also helped smarten up the way we organise work so everybody knows what they are doing and things work a lot smoother. They have really helped my business and I’m looking forward to working with them again.
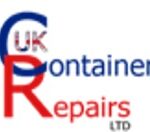
What are the benefits?
Achieve your objectives
Our targeted approach ensures efforts are focussed on delivering real, measurable and sustainable results aligned to your company goals.
Detailed process insight
Taking a systematic and structured approach, we produce a comprehensive gap analysis of your operations. This analysis provides you with thorough insight into your processes and operations.
Deliverable project plan
A project plan ready to go, specifically designed to achieve your objectives. Structured into standalone work packages that deliver measurable and sustainable change
Improved profitability
We employ Lean Manufacturing techniques to remove waste and improve flow, resulting in a more efficient, balanced and profitable line.
Improved product quality
With Six Sigma you can unlock the true value in your process by enhancing quality. Make your customers happier by reducing product defects and time spent reworking errors.
Deliver New Capability
Open new markets by offering new capabilities. Making sure you have the right equipment can be tricky and expensive, from detailed specifications to smooth handover to operations we are here to support you every step of the way.
Why Us?
Our team are experts in Process Improvement and process scale-up with backgrounds in Science, Engineering and Manufacturing. We offer our knowledge and experience to help you get it right first time and on time.
We have collectively saved small and medium sized businesses in excess of £10M over the last ten years. The key to this success stems from pursuing a deep understanding of how the business works, what it is trying to achieve and working out the steps to get there.
We can work as part of a team to deliver well defined improvement projects or independently to help drive improvements across your business.
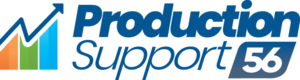
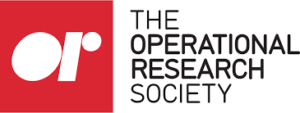
Getting started
The day job of many manufacturing organisations is to make sure that the right product with the right quality is produced on time for their customers. Keeping up the pace of production on a daily basis to meet production targets is often the principal aim of production, leaving little or no time to identify and implement opportunities for improvement.
At production Support 56, our Process improvement specialists are dedicated to helping you with your improvement projects so you can get the most out of production and support you to deliver your operational growth plans. Our support takes the strain and hassle over identifying improvement opportunities, providing practical solutions, and delivering a clear and timely implementation plan.
Our team take an analytical approach to all projects and work together with you at every step of the journey.
Planning – project scope, business needs analysis, gap analysis, mapping the value in your process, targets, goals, kpis and constraints.
Doing – problem solving and solution finding, testing the solution real world in a controlled fashion.
Evaluating – measuring the benefit of the change – did it work.
Implementing – making it the new standard – procedures, training, quality control mechanisms