Simulation for Improvement
Unleash the potential of your processes with Factory Simulation.
We create an accurate digital twin of your production facility using real operational data. This helps Operational Managers identify weaknesses in their line, virtually test any change and helps avoid those costly mistakes.
Arrange a free demo

What is Simulation for Improvement?
Simulation for improvement is used to create a digital representation of your production facility which captures all the performance characteristics of your equipment and resources. It accurately replicates your raw materials and products as they move through your manufacturing lines giving you a realistic and precise reflection of daily production. A major benefit of using simulation is that the model tracks both the status and performance of your equipment with time, so, if you wanted to understand the reasons why performance crashes on a Thursday afternoon you can look with just a few clicks of the mouse.
Process Mapping
The simulation is based upon a process map of your production facility. The map can be high-level to compare conceptual ideas or highly detailed to calculate accurate and up to date operational costs to the nearest penny or kilowatt.
The process map describes how your individual activities are linked and how product and information flow through your production system. Each activity is described in terms of capacity, cycle time and resources required. The resource availability is also defined and acts as a constraint on the simulation, precisely reflecting real world operations.
Gap Analysis
Understanding the current performance of production is of critical importance. Once you have an accurate measure of current productivity can you then take steps to improve it, without the baseline information it can be impossible to know if any improvement has actually made a positive impact.
A fundamental feature of any process improvement activity is to have a gap analysis which compares current performance against a known target. Once this gap is understood solutions to bridge the gap can then be made. Conducting a gap analysis can seem like a daunting task, getting the right information, ensuring its accuracy and having the time to complete it can mean many hours spent staring at complex spreadsheets trying to make sense of the data.
What great about simulation is that once your model is built, you are instantly provided with a clear picture of the current performance backed with accurate data. The model pinpoints exactly where areas of the process are in need of improvement which helps you to define which projects need immediate attention.
Process Optimisation
Once you have the simulation of your current factory you can start to explore potential improvement opportunities and ask those ‘What if’ questions. You may want to look at the effects of different shift patterns, changes to the skills matrix, evaluate new equipment, new products or new layouts. In fact, you can model and test practically any change you can think of. The simulation will provide you with accurate and clear performance data on each scenario and every combination, allowing you to make decisions with confidence.
Using your model, you can then test as many solutions as you like. With just a few clicks you can make changes to your production line to test out your ideas, re-run the simulation and compare the results directly against your current operational performance to determine if the improvement has made a positive impact.
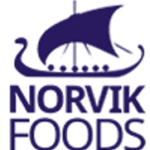
The Benefits of Simulation for Improvement
De risk decision making
Since the model is constructed using real process data, operational decisions can be made with clear and unbiased data-based evidence rather than relying on instinct or hunches.
Obtain accurate costs
Your model tracks labour, energy and material usage. With just a few clicks of the mouse you can get accurate costings and carbon footprint of any production scenario you can think of.
Identify the big wins
Your model and inbuilt analytics means improvement opportunities can be immediately identified and quantified. Potential solutions can be rapidly tested and outcomes evaluated.
Test ideas risk free
Stress test, develop and optimise your plans without any risk. Stakeholders can interrogate your growth plans, building confidence and establishing consensus.
Clear process understanding
Your simulation provides a visual representation of your processes, which brings clarity to complex processes. You can bring Improvement ideas to life and see the future in action.
Design efficient processes
Avoid the unnecessary stress and worry over critical process design decisions far in advance. Test your ideas beforehand to remove process bottle necks, balance production, schedule production and maximise flow.
Why use Production Support 56?
At production support 56 we have decades of experience working with operations and production teams developing and optimising processes. We first used simulation to justify capital expenditure of expensive process equipment. The simulation demonstrated that the equipment had the right capacity for the sales forecast and resulted in high utilisation and good value for money.
We have a background in process improvement and manufacturing and found simulation to be an excellent supporting tool. Our background ensures the models are realistic and behave accurately under simulated stresses. We typically identify opportunities to increase throughput by 10% before any capital investment. Find out more about us here.
We are accredited by Simul8 as a certified solutions provider and use their state of the art software to create and run simulations of your design. This powerful software platform allows us to focus on getting the right information into the model, and more importantly provides the means for producing meaningful analysis.
How to Get started with Simulation for Improvement.
Production Support 56 can support your improvement project by creating a computer simulation of your production facility. The simulation can be used to assess current performance, test out improvement opportunities and communicate these to stakeholders within the business.
To create a simulation, we follow these steps:
- Project Goal - Define immediate needs of the business and longer-term goals. For example, increasing throughput, adding capability like new product lines or upgrading existing equipment. The goal will define the focus of the model.
- Data collection- Create process maps and collate performance data of your facility. Collect historic production or sales forecasting data.
- Model- Construct a bespoke computer model using state of the art manufacturing simulation software.
- Validate and test- Together, we interrogate the model to identify inefficiencies and where simple gains may be found. Carry out predictive simulation testing on proposed changes or improvements to prove the value of the change. For example, new equipment, staff deployment, or plant layout.
- Report- Collate and report out key findings and information from the model.