Simulation for manufacturers is a fantastic tool . It allows you to solve operational problems digitally without making physical changes. It allows you to test your limitless ideas and quantifies and compares the potential outcomes. It allows you to identify the best operational plan to meet your goals.
This article is written for people working in Manufacturing who are interested in understanding how simulation can help them do a better job.
What is simulation?
So, before we get into the pros and cons of simulation, let’s start with what is Simulation?
‘Simulation is the process of designing a dynamic model of an actual dynamic system for the purpose either of understanding the behaviour of the system or of evaluating various strategies (within the limits imposed by a criterion or set of criteria) for the operation of the system.’ Ricki G. Ingalls 2008
The simulation is a dynamic model of your operation. The model, if made properly, will behave in a similar manner to the real one- it will simulate real life behaviour. And because the simulation behaves in a similar way to the real one, we can ask it operational questions and get useful answers. Would automating a process help with throughput? What is the optimum shift pattern? What level of inventory should I carry? And when we want to communicate these ideas, the visual nature of simulation helps all stakeholders see the plan in action.
To make our life easier we only model the elements of the operations that are relevant to questions we want answering. If we are looking at how work moves through our production lines, we would generally only model equipment being busy or idle. If we wanted more detail, we may also model the equipment waiting for resources, broken, or being changed over. How the equipment is used, which buttons an operator press, is generally irrelevant to the question and so is left out. Likewise, an accurate 3D spatially correct model may look great, but does it help you identify the best shift pattern. We all have too much to do with too little time, so the key is to only model what you need to model to give you the answers you need.
You may have used spreadsheets to model elements of your operations. These are great and can give you the answers you need quickly. However, these are static tools and will only give you static answers. If you need to know what is going on with production each Tuesday afternoon after the first break, or how the inventory levels vary through the day then you need a dynamic tool.
There are several different types of simulation available. For example, discrete event simulation, systems dynamics and agent-based modelling. Due to the nature of manufacturing, where things typically occur as a series of activities, we find that discrete event simulation fits really well. There are of course exceptions, if you are looking at high level operations or conceptual ideas then systems dynamics may be better. If there is a high level of autonomy, then an agent-based model would be better employed. For the rest of the article, we are only going to consider discrete event simulation.
Discrete event simulation (DES)
How best to describe discrete event simulation? I’ll start by quoting somebody else:
‘In discrete-event simulation only the points in time at which the state of the system changes are represented. In other words, the system is modelled as a series of events, that is, instants in time when a state-change occurs.’ Stewart Robinson Simulation- The practice of Model Development and use.
Basically, you are just modelling when changes to your system occur. The simulation is a series of instantaneous system changes with delays in between. What I find interesting is that when a piece of equipment in your simulation becomes busy, the software does not give it any more importance than if the equipment was idle. The software just cares about when these changes occur. It is up to the manufacturers to define what is important to them, and set-up the simulation to record and display the important data.
How a discrete event simulation is created
It might be easier to give a better explanation of what DES is by describing how you create a model. You create a process map of your operation using the elements in the software. These elements are the building blocks of your process map and creates the logic of how your material, customers and information flows. You define the important properties of each element, for example how long a job takes, how many items can fit in a hopper, what activities a job role can do. You also define what information you want the software to collect, some common statistics will automatically be measured, such as busy and idle times of equipment, others will have to be defined.
The model starts when an entity enters your model. An entity is the thing that work is done to, and it can be material, customers, or information. The entities flow through your process map in the way described by the model’s logic and properties. As entities flow through the process map it triggers discrete events.
Discrete events are the points in time when the state of the systems changes. The simulation ends when it is timed-out or the last entity leaves the model. When the model has finished you can access the data generated by the simulation. The software creates a schedule of discrete events for a scenario. As a user you can pause, fast forward and rewind the simulation. You can move to any time in the simulation and take a look at the current status and statistics.
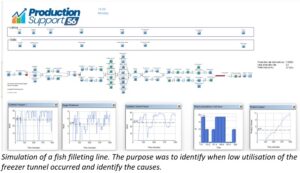
For those of you who work in manufacturing, you can probably see why DES is such a good fit for simulation manufacturing processes. Most products move through a factory in a fixed sequence of unit operations. The resources and processing time required for manufacturing are specific to a product and can be easily defined. Most individual production decisions can be described in an algorithm. The properties of each individual piece of equipment can easily be described. It is only when you put all these simple elements together that you find you have a complex system which is hard to predict. This is where the software takes over. DES software was designed so that you can build your operational simulation from these simple elements, and then use computational power to run the complex system as a series of discrete events.
Once you have created your model you can then provide it with scenarios and allow the simulation to predict how they will play out. If you want to see some examples of Simulation for Manufacturers then check out our YouTube channel.
Pros and cons of simulation
There are huge benefits of simulation for manufacturers but let’s not kid ourselves that it is easy. Let’s start with a list of cons:
· You need specialist software.
· You need to know how to use specialist software.
· You need to dedicate time and resources to create simulations of your operations.
· You need a detailed understanding of your products and processes.
· You need a good understanding of statistics.
As manufacturers, even if you don’t think simulation is for you, you should be working on the bottom two bullet points. If you are still sitting on the fence, then let me tempt you with a list of pros:
· You can interrogate complex operations.
· You can make evidence-based decisions.
· You can identify and quantify best solutions.
· You can identify bottlenecks and weaknesses.
· You can pinpoint failure mechanisms.
· You can visually communicate investment plans.
· You can build confidence with stakeholders.
· You can quickly test new ideas and scenarios.
· You can ensure efficient use of capital spending.
· You can generate accurate activity-based costs.
· You can uncover hidden risks in new plans.
How do I get started?
If you are a manufacturer and think simulation could help your business, then get in touch with us at Production Support 56 and we’ll arrange a video call to help you get started or take a look at our Simulation for Improvement page